(from my perspective – Yannic)
Keybrick started with a call from my friend Till some time in early November 2019. Till had bought his son a LEGO® City passenger train set a few weeks earlier and quickly got fed up with the growing pile of depleted AAA batteries on his desk.
With about three and a half hours of play time they were munching through the AAA batteries, six at a time, at an incredible pace. After a failed try at using rechargeable NiMH cells came the said call….
Do you think I could somehow connect a Lithium battery to this Hub?
Till – early November 2019
After a brief investigation I decided to fire up my CAD programm to draft a first shell for what was to become Keybrick:
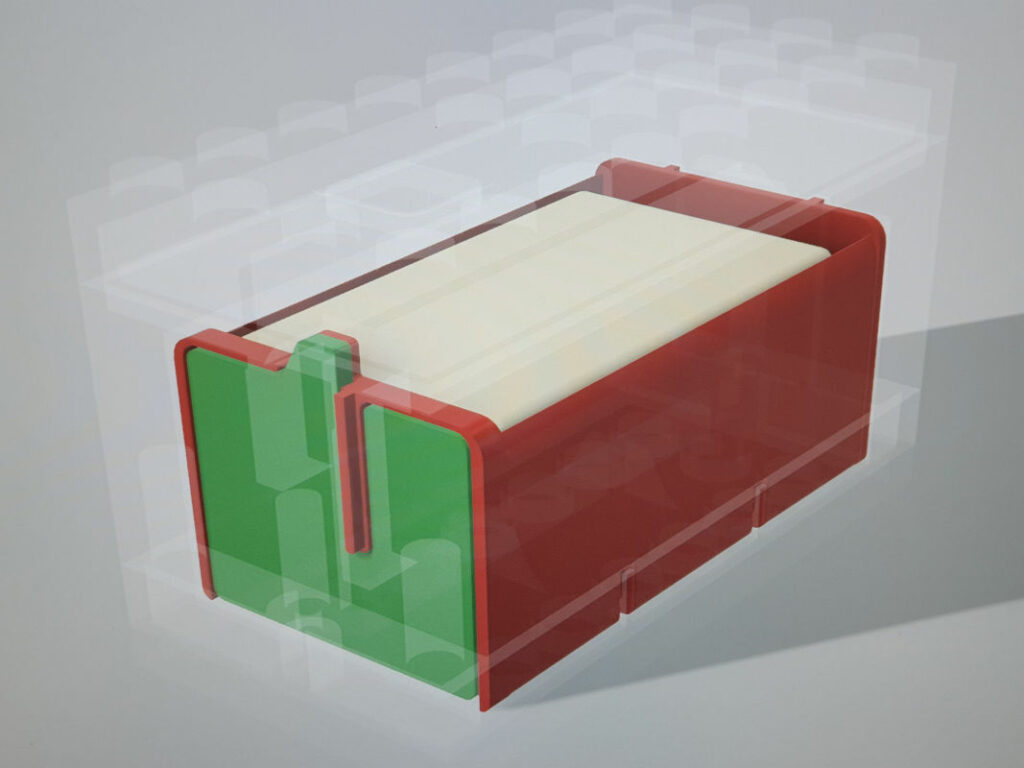
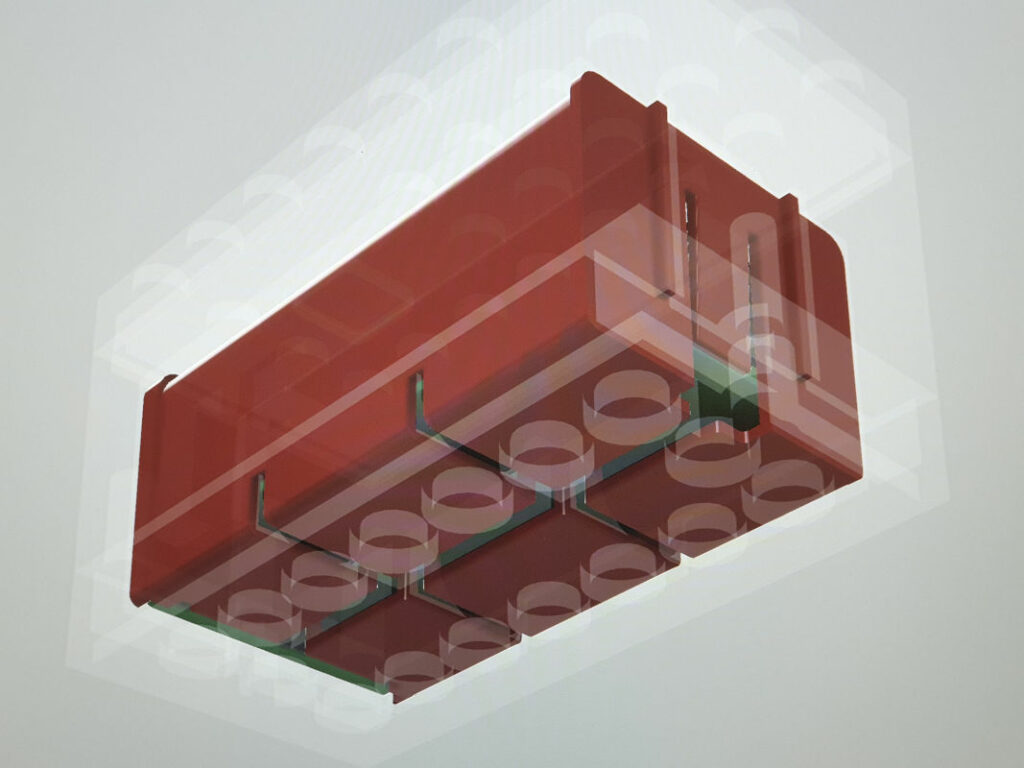
That first try was designed to replace only the battery holder inside the original LEGO® Powered Up hub.
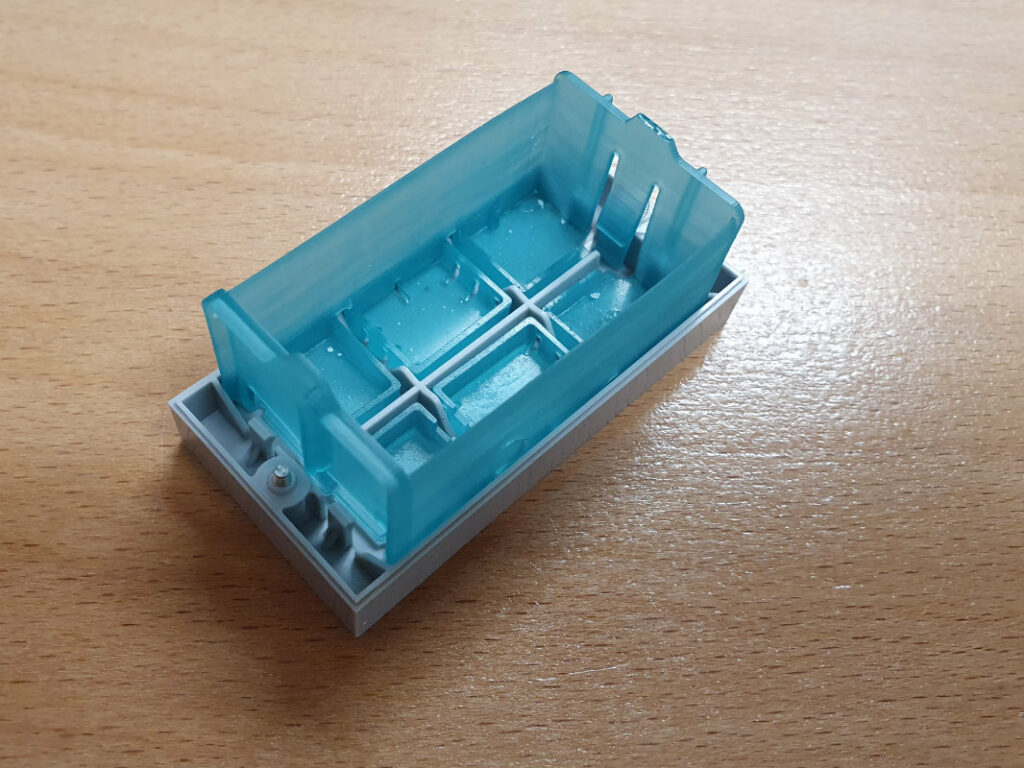
Then came the first PCB and working prototype for what we called PowAAA_Brick at the time:
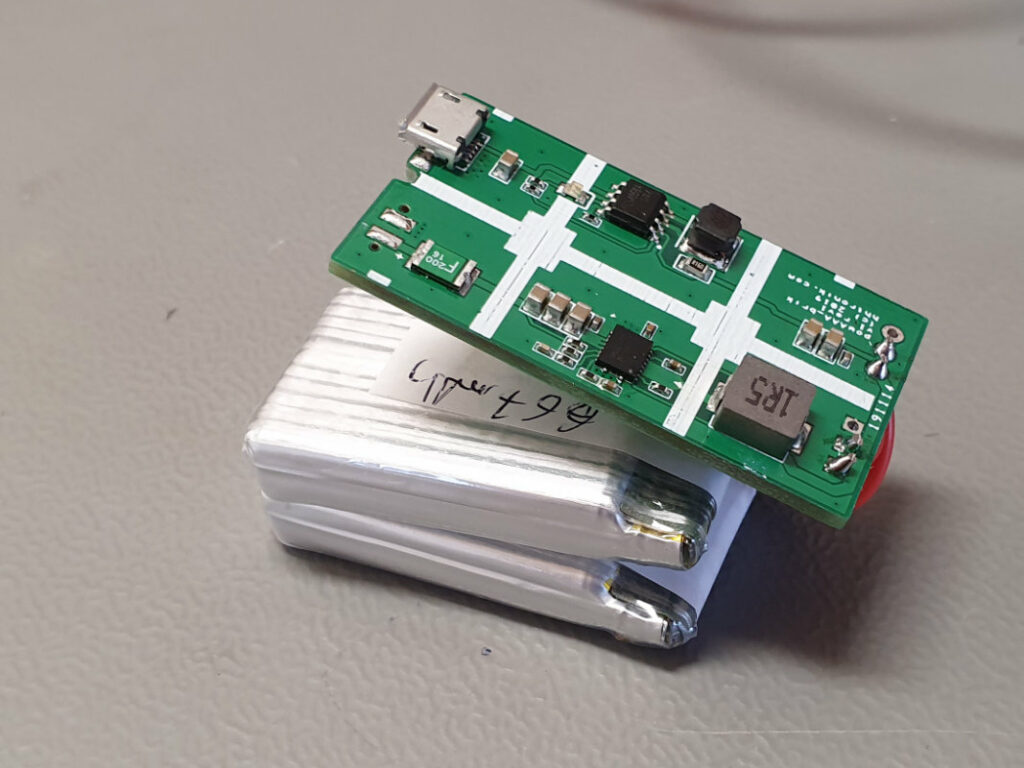
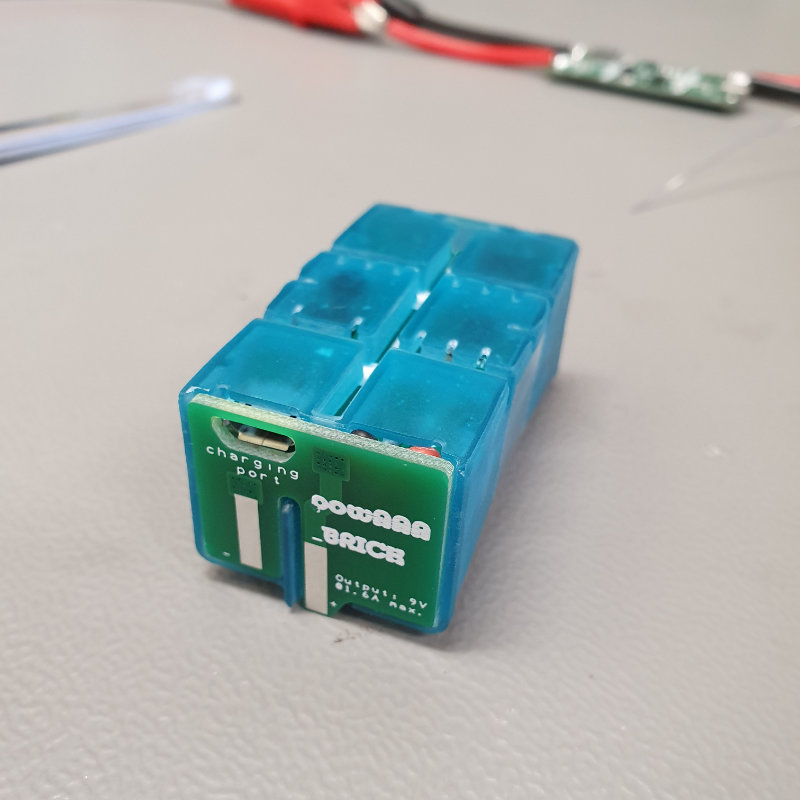
Then followed a few more revisions and prototypes:
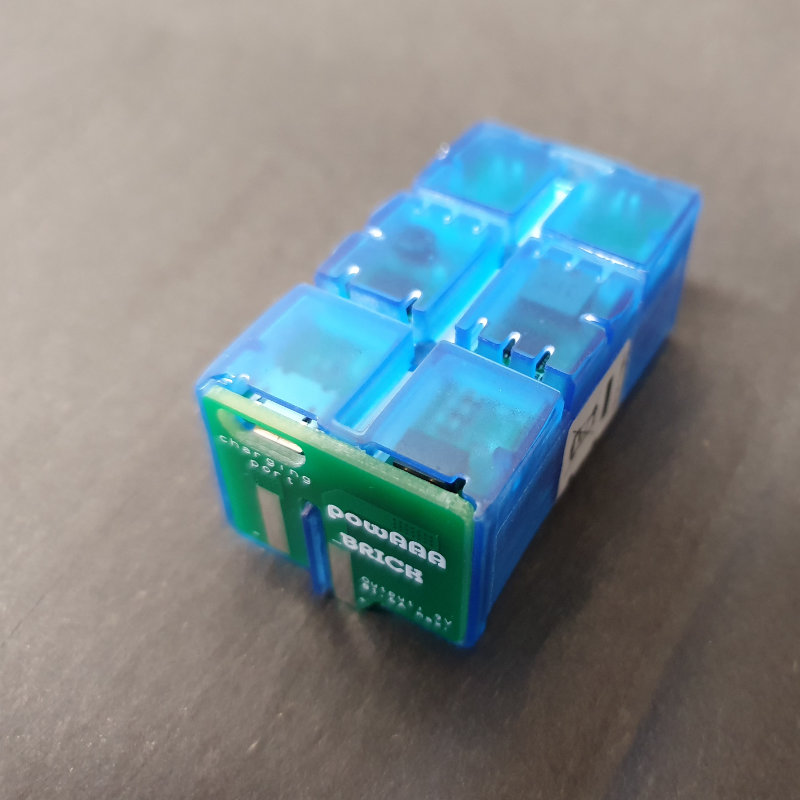
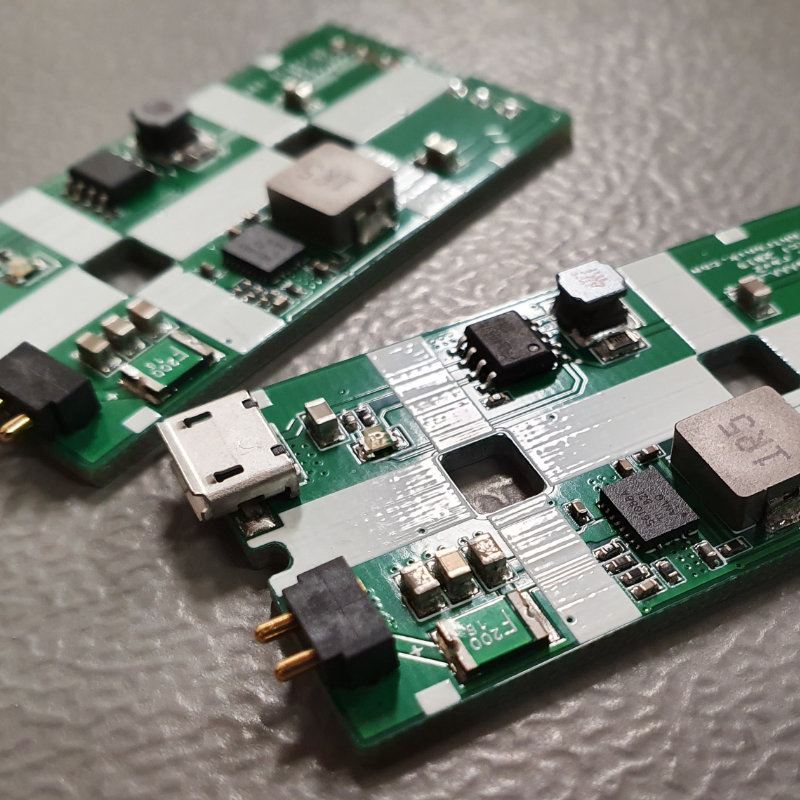
At this point we had early 2020 and decided that it was worth taking the whole idea one step furthers by designing an injection molding compatible enclosure, this time replacing the whole lower part of the LEGO® hub:
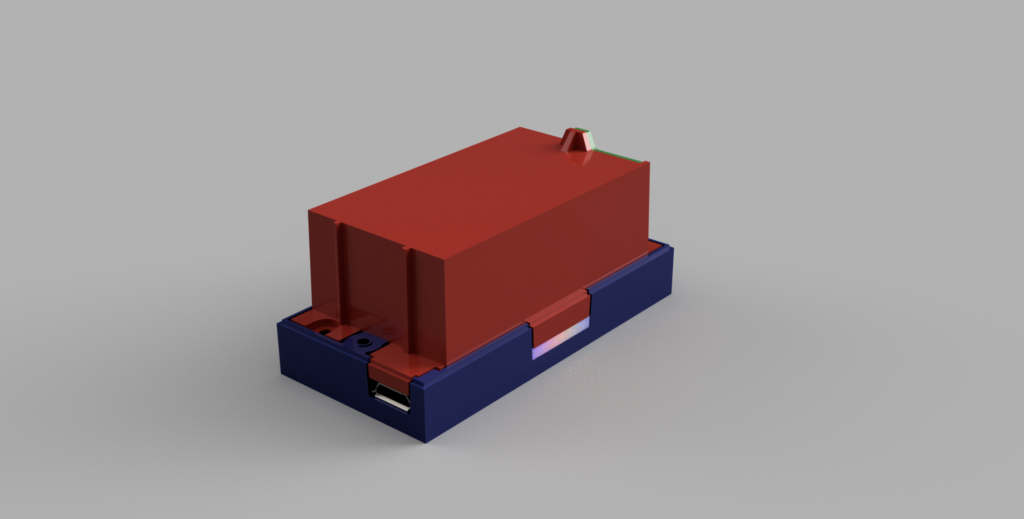
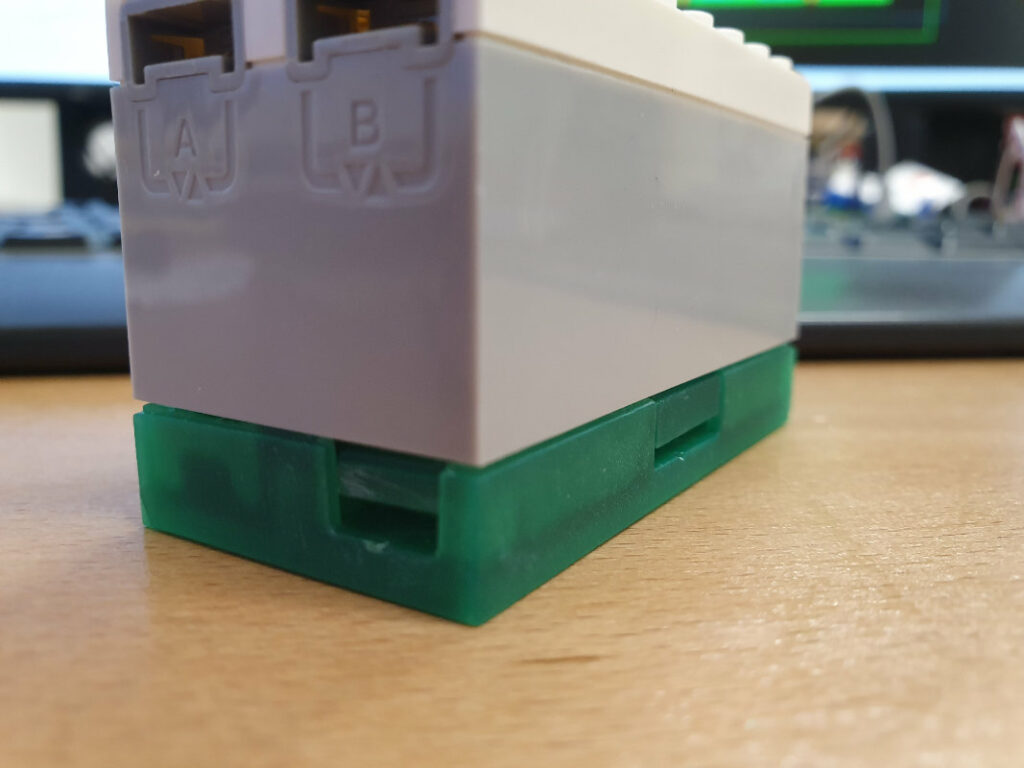
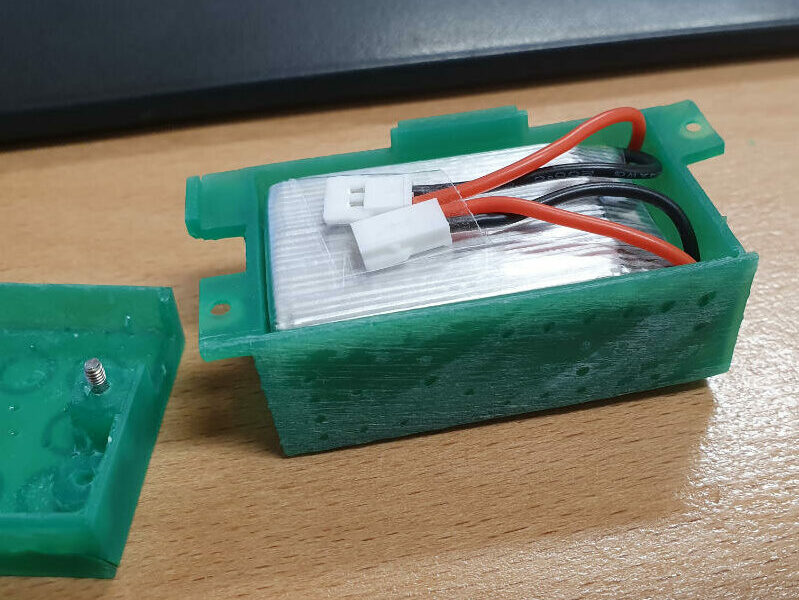
This change was pushed by the feedback of our early testers. They complained that the original concept was too easy to put in “backward” and that the charging procedure was as annoying as changing the AAA batteries in the original.
Additionally to getting the externally accessible micro USB port allowing you to charge Keybrick without having to take it out of the hub, this iteration added our signature rainbow status indicator light!
In April 2020 I had the first case manufactured using a polyjet 3d printer and polyamid 12 as a material for evaluating mechanical properties of a stronger material.
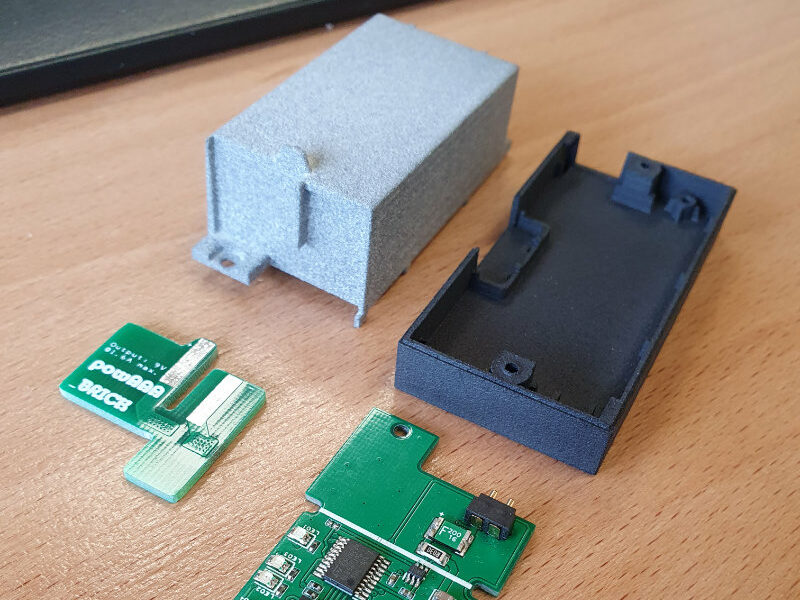
Later in April we renamed powAAA_BRICK to Keybrick and had a few more iterations of the PCB (better thermals, much better stand-by performance…). A lot of programming and some laser cutting, we got to this point:
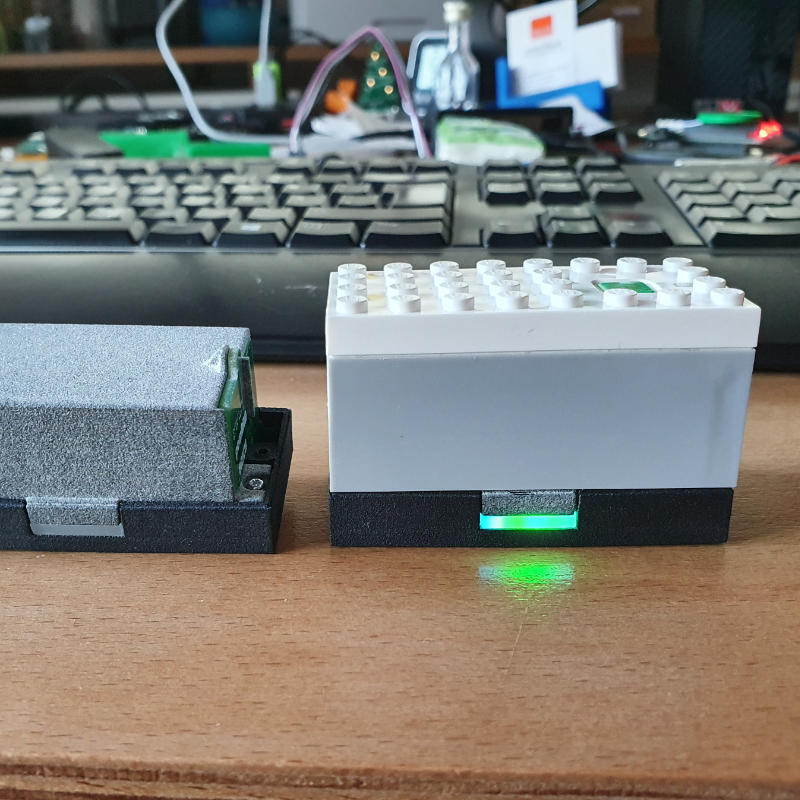
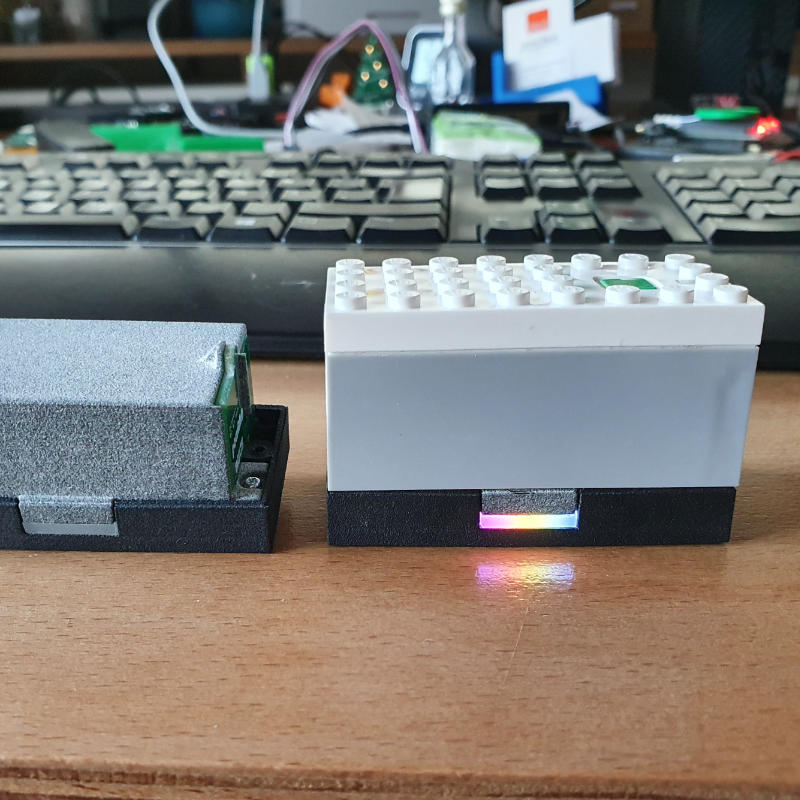
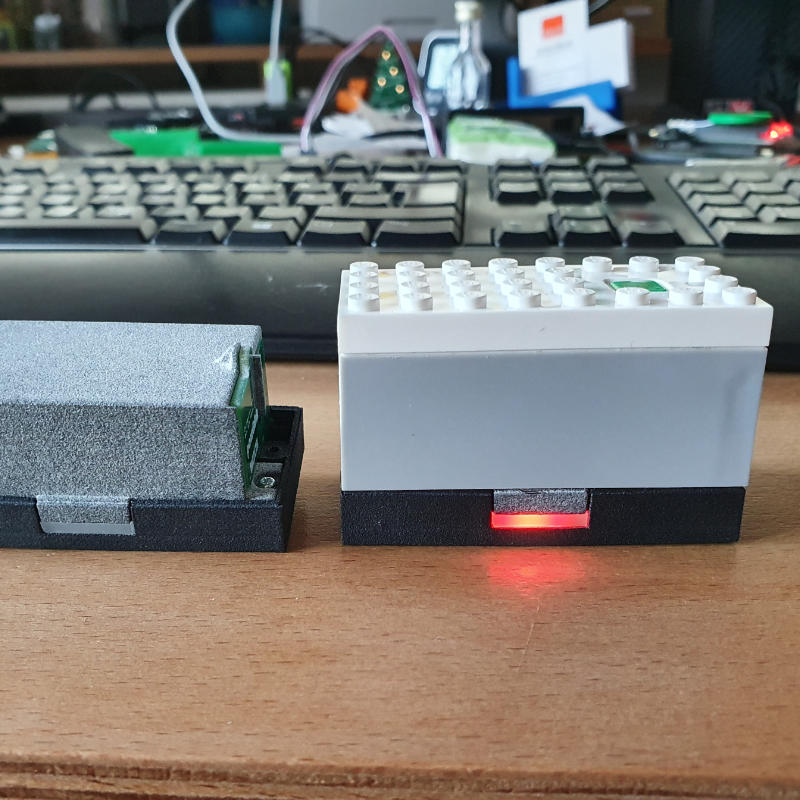
We did a LOT of testing since revision one: be it drop testing Keybrick, over-loading it, shorting it out, completely draining it or EMC testing, we’re confident that Keybrick is up to very high standards already!
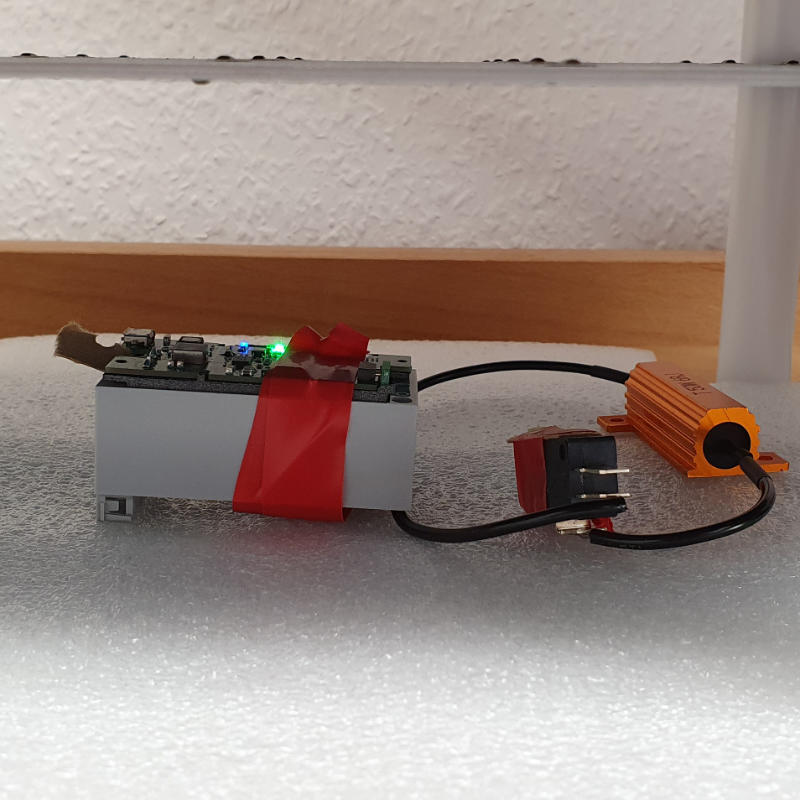
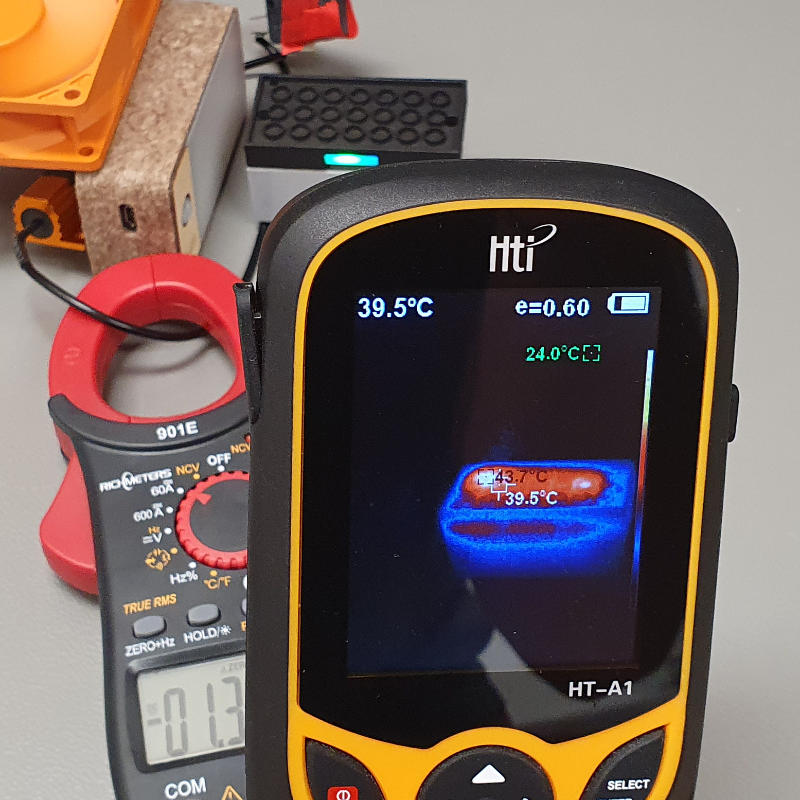
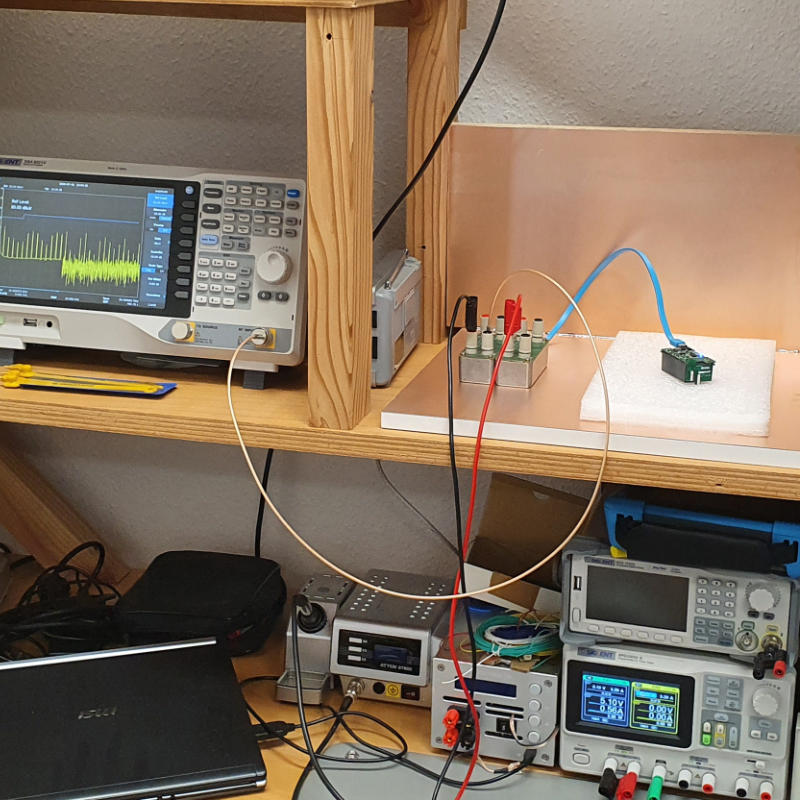
The latest prototype of Keybrick looks like that:
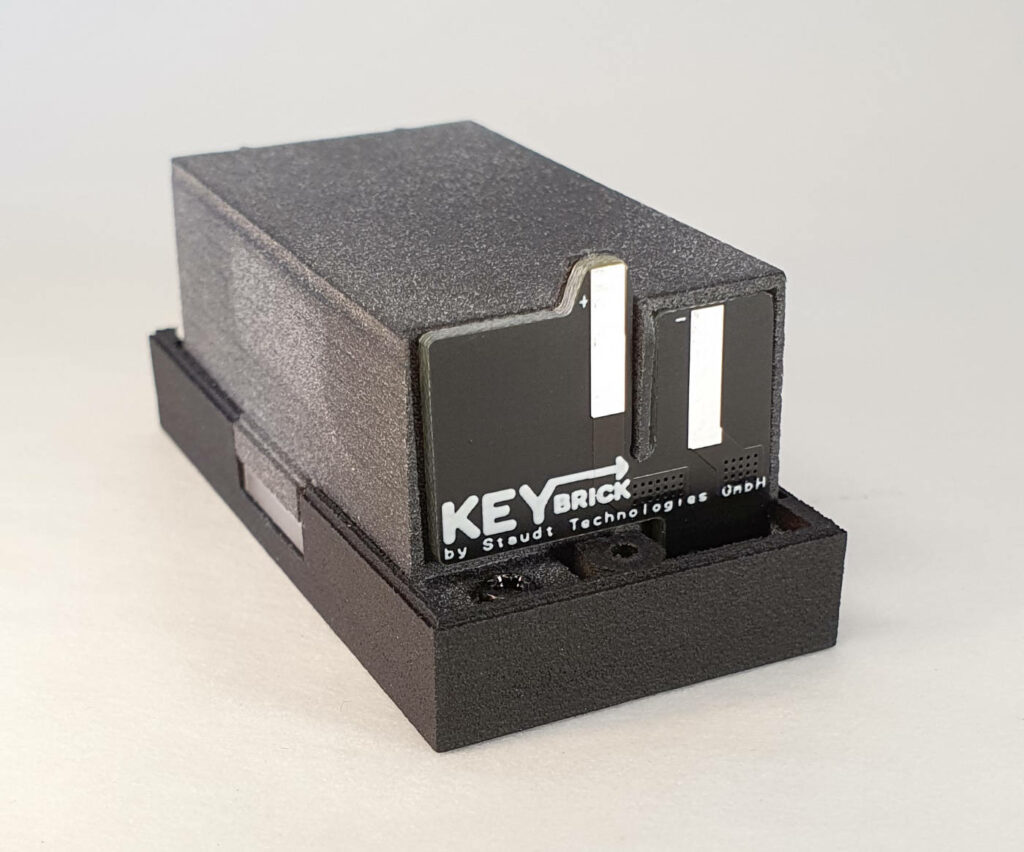
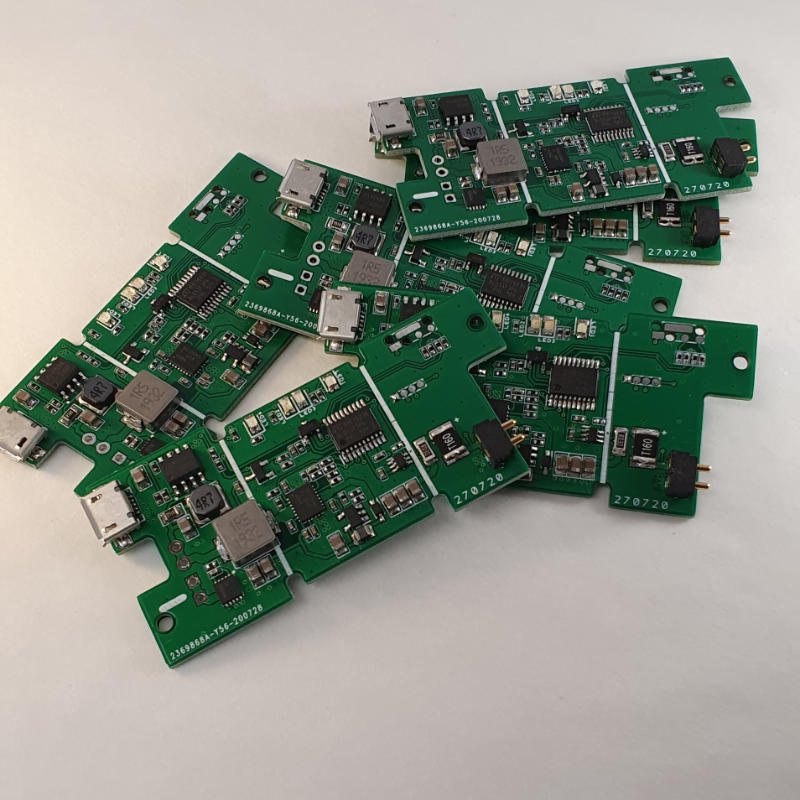
The new PCB includes an on-board battery protection to make sure Keybrick is safe. We decided to built that into our own PCB for packaging and cost reasons after discussing options with our LiPo-cell provider.
As I’m writing this (August 12th 2020) there’s a package of sample battery packs on their way to me for final fit testing and validation of the production grade custom made cells.
The Kicksarter Campaign
We launched a Kickstarter campaign for Keybrick One in late September of 2020. Unfortunately it didn’t reach our set target but we learned a lot. If you want to have a glance of where we come from, head over to the campaign as it’s a great place to start the discovery.
Nevertheless we produced 40 Keybricks for those who were up to support our Kickstarter and absolutely wanted a Keybrick.
At this point thanks to all who belived in Keybrick and our vision!
And then?
Well, you all know what happend in this time frame 2020-2022? The pandemic!
The world stood still, lockdowns, quarantines, no flights, no logistics, no chips, no production. Especially the global chip shortage was hitting us hard and we couldn’t go on as planned with further production of Keybricks.
Resart 2023
(from my perspective – Katharina)
As you may noticed, now it’s me Katharina who is writing the text.
I had to decide on going back to my old employer with all the advantages and disadvantages or shoud I step in a 100% to Keybrick (with all the advantages and disadvantages). Long story short I resigned from my former job and do Keybrick instead.
I started in February to become acquainted with the production of Keybrick One. Together with Yannic who explained everything to me I was able to do a first batch of Keybricks Mid March. They were sold out within 2 Weeks!
The 2nd batch was 95% done by me just with a little help and was online End of May. Sold out whithin 3 weeks.
Upgrades 2023
During summer I worked a lot. We had to fill up our stock.